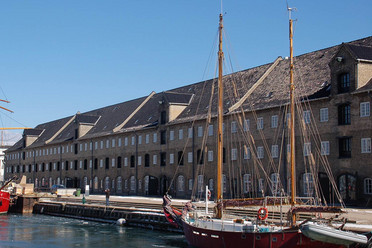
devA
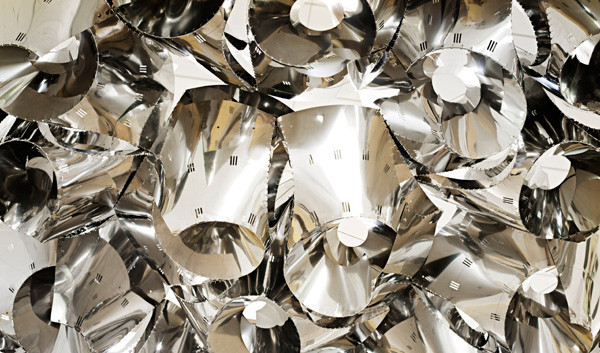
A research collaboration between CITA and MAPT.
The DevA research project investigates the use of curved sheet material in architecture using hybridised 3D modelling and pattern cutting techniques. The project explores how digital design and fabrication technologies enable the development of new structural concepts through the new means of material specification and detailing at unprecedented levels of precision.
The project employs a practice based hand-on method based on the development of speculative probes, material protoypes and demonstrators. This method allows us a direct insight into the techniques and material properties in working with steel anddevelopable surfaces.
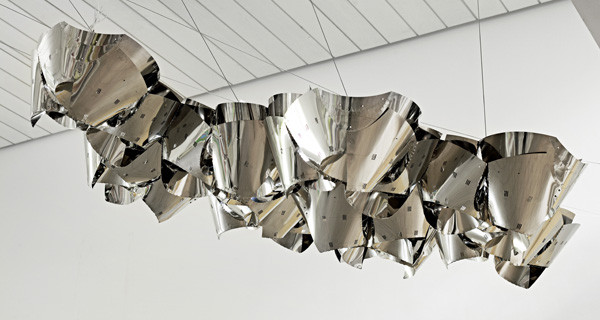
Structural Skin
The project has been developed through a series of collaborations. Established as a collaboration between CITA and MAPT it involves architectural academic and practice environments. Further collaborators from academia and industry have been fundamental in the development of the project. The research collaboration with Kristoffer Joseffson at the Institute of Mathematics at the Technical University in Berlin has been instrumental in the mathematical investigations. Industry collaborations with Lars Moth Poulsen from Bentley Systems, Denmark and the Ide-Pro Dassault Systemes software in Denmark have been key to the modelling of the surfaces. We also thank Preben Brandt and Ib Lindskov Hansen at Beyer Teknik ApS for their support in laser cutting.
Architecture is mainly made of planar elements. Sheet materials form the basis for most building elements both as direct planar materials such as façade claddings and interior walls as well as folded materials such as steel profiles or rolled materials such as air vents. The ability to bend and fold sheet material has been exploited mainly in metal based formwork. Where some examples from early ship making and furniture design have developed techniques for bending and laminating wood, it is in the steel industry that huge advances have been made through complex form making.
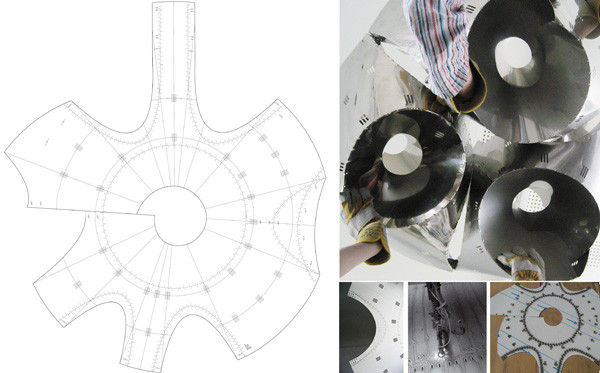
The starting point for the DevA research project is an interest in structural skins. The aim is to investigate how developable surfaces and the techniques for unrolling these surfaces can be used to develop structural membranes. Choosing steel as a material allows the project to engage with an architectural scale of investigation as well as material knowledge from the building industry. The project asks: what are the structural behaviour of bent steel sheet and how can it be used in architectural design? What are the appropriate material traditions and how can we learn from other disciplines such as textile flat pattern making? Are these techniques scalable and what happens as be move from compressive to non-compressive materials? And finally, what are the design potentials and embedded expression of bent steel constructions?
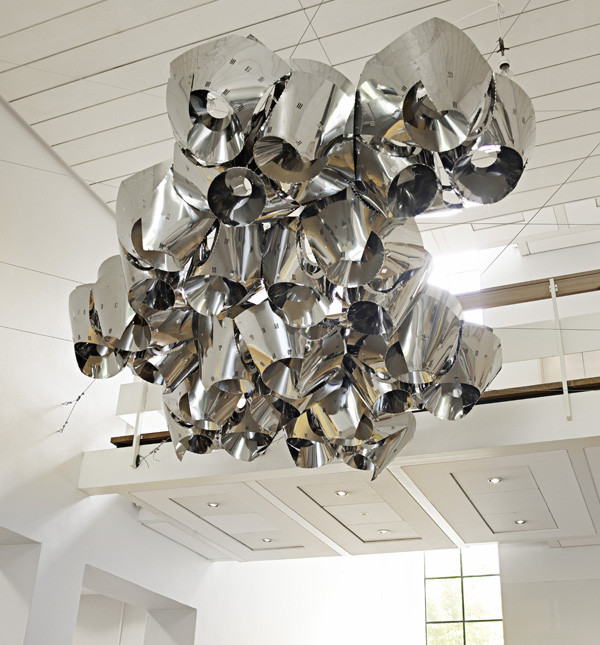
The starting point for the DevA research project is an interest in structural skins. The aim is to investigate how developable surfaces and the techniques for unrolling these surfaces can be used to develop structural membranes. Choosing steel as a material allows the project to engage with an architectural scale of investigation as well as material knowledge from the building industry. The project asks: what are the structural behaviour of bent steel sheet and how can it be used in architectural design? What are the appropriate material traditions and how can we learn from other disciplines such as textile flat pattern making? Are these techniques scalable and what happens as be move from compressive to non-compressive materials? And finally, what are the design potentials and embedded expression of bent steel constructions?
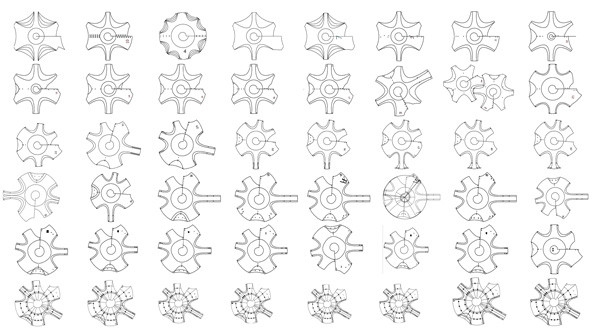
Developing the patterns
The interest in pattern cutting comes from a series of projects that have explored the relationship between flat pattern cutting and architectural design. The interest here is the fundamental difference in understanding the drawing, or the pattern, as a material description to understanding it as a representation. Where architectural traditionally understands the drawing as an orthogonal cutting of the building body, a slice that in turn reveals it section and layers to the builder, the pattern in a material descitpion that goes along the body of the built, and in which the details of the material are detailed. The pattern is a such a part of the construction of the material – it describes directly the material extension of the envelope.
The second idea that DevA engages with is the idea of material self bracing. Learning from the textile logics of these project we have become interested in how materials gain structural strength when set into tension. This notion is already incorporated into architectural and engineering practice through pre-tensed materials. In textile thinking this incorporation of material tension is fundamental. The structural performance of a textile is exactly the tension that happens through yarn to yarn friction, but also in the yarn it self through fibre to fibre friction. Working in close collaboration with a small scale steelwork company the 2D pattern were laser cut in 0.7mm steel sheets. Through material testing we found that thin steel could bend in ways that were comparable to the cardboard models generated in the design process. We developed a stitch like pattern replacing the scoring of the material allowing for a frictionless bending of the steel sheeting.
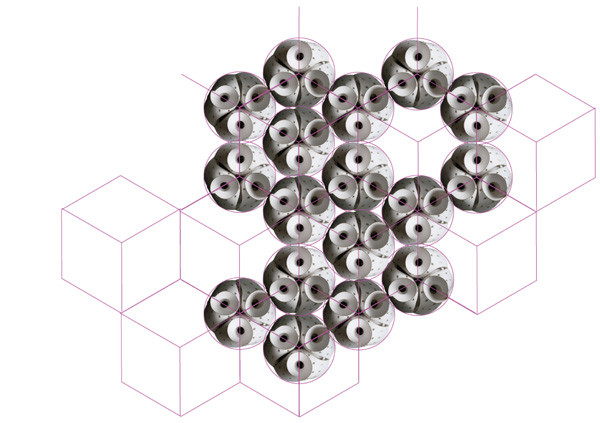
The clustering of the components is structured around two nested layers. In the first layer, three components are joined in a “pod”. The pod is structurally integral joining the three components by introducing further convex creases into the surface. These creases allow the components to pack together tightly assemble together so that they can be bolted together. By lengthening on side of the pattern we furthermore developed a central core, or “column”, that is used to strengthen the connection between the components.
At the secondary level the pods are packed together in a hexagonal matrix. The pods are bolted together using the same system of secondary crease lines. During the testing of the assembly we found that the pods were slightly twisting the overall surface creating further tension. To compensate we reversed the bending of every second pod using the backside of the pattern. In this way the tension is dissipated rather than accumulated each pod slightly twisting against the next.
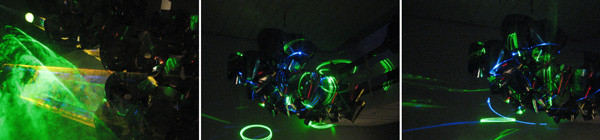
The final demonstrator Reef Pattern was developed for the Distortion Festival 09 and presented at Kunsthal Charlottenborg in June 09. We thank Thomas Fleurquin and his team for their support and interest.
Publications
Tamke, M., Ramsgard Thomsen, M., Asut, S, Joseffson, K.
"Translating Material and Design Space - Strategies to Design with Curved Creased Surfaces"
Proceedings 27th eCAADe conference, september 16-19, 2009